Materiali performanti, ripetibilità industriale e di più: sostenibilità, resilienza.
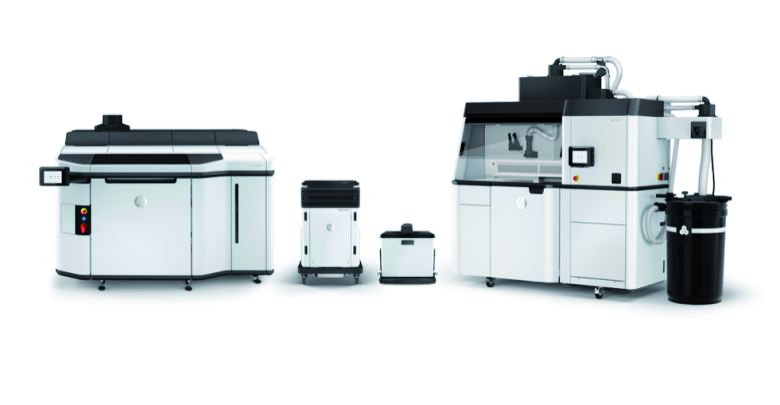
demand. Nella foto, il sistema Multi Jet Fusion di HP.
Il tema della produzione on demand e della sostenibilità sono centrali in questo momento di crisi dell’industria: i miti della globalizzazione e della reperibilità immediata e capillare dei beni di consumo di massa non hanno retto all’imprevisto di questo biennio di discontinuità e rincari di materie prime e servizi.
La rapidità e la complessità non sono più i soli vantaggi distintivi dell’additive manufacturing; le alte prestazioni dei materiali e la ripetibilità dei processi l’hanno resa anche autosufficiente e sostenibile. Le tecnologie di manifattura digitale hanno rivoluzionato il processo di design, ripensando l’uso dei materiali, di strutture e forme, in una logica di organicità ed economia virtuosa. Inoltre, per via additiva i componenti di macchinari e di prodotti consumer sono riproducibili a basso costo; il materiale consumato è solo quello che occorre e la supply chain è tutta a portata di clic, senza stampi, scorte di magazzino, scarti.
Innovazione di ‘laboratorio’
Quanto e come la manifattura additiva si sta integrando nell’industria? A fine 2020, HP ha consultato i decisori che all’interno delle aziende si occupano di digital manufacturing e 3D printing. L’89% ha dichiarato di trovarsi in una fase di cambiamento dei modelli di business, in cui sta valutando sistemi di produzione innovativi e sostenibili. Il marchio Decathlon utilizza due stampanti Multi Jet Fusion di HP presso l’ADDLAB, un laboratorio che produce pezzi di ricambio per i propri prodotti, prototipi, validazione dei design, piccoli utensili. L’introduzione dei metodi additivi ha permesso di ottimizzare il flusso di lavoro, di indirizzarsi verso nuove applicazioni e di ridurre l’impatto ambientale. L’Oreal ha impiegato la soluzione di HP per progettare e produrre rapidamente grandi volumi di supporti (in gergo “puck ”) regolabili per trasportare, confezionare ed etichettare i suoi prodotti realizzando una riduzione dei costi del 33% e un risparmio di tempo del 66%. La capacità di personalizzare i supporti è stata efficace anche nell’assecondare con agilità le mutate abitudini di acquisto dei consumatori durante la pandemia di COVID-19.
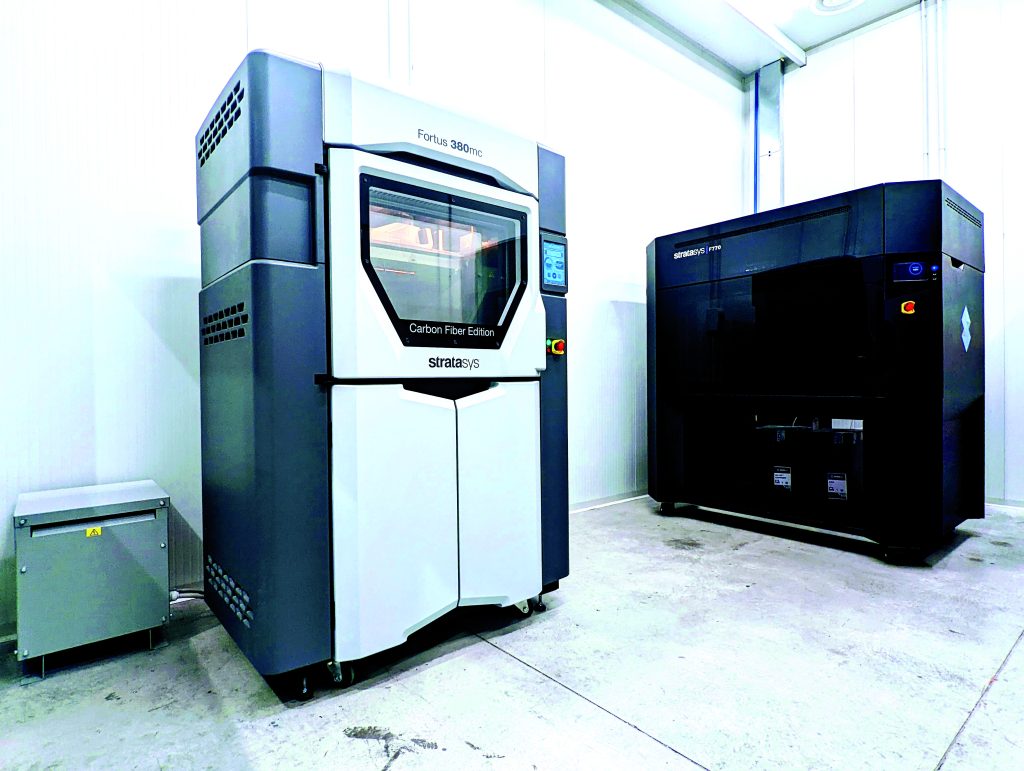
di carrozzerie esterne e interniper Ferrari, Stellantis, BMW.
Nell’industria automotive un design più originale e seducente può rapire l’acquirente alla Casa concorrente. Il gioco è in mano ai centri di progettazione come SuperStile, che sviluppa carrozzerie esterne e interni per modelli concettuali, prototipi funzionali e show-car di Ferrari, Giugiaro, Stellantis e BMW. Per soddisfare la domanda di applicazioni per parti dettagliate di grandi dimensioni, l’azienda ha installato la stampante FDM (Fused Depositon Modelling) F770 di Stratasys, caratterizzata da una camera di costruzione riscaldata, particolarmente efficiente, che misura 1000 x 610 x 610 mm, e dalla disponibilità di materiali resistenti, prestazionali ed estetici. I termoplastici ABS-M30 e ASA sono già stati utilizzati per stampare in 3D diversi modelli di specchietti retrovisori, maniglie delle portiere e bocchette di ventilazione. “L’acquisto della stampante 3D Fortus 380 di Stratasys nel 2021 ha indotto una trasformazione radicale della nostra mentalità e dell’approccio complessivo ai processi di progettazione e sviluppo. – osserva Franco Palmisano, co-fondatore di SuperStile – Accanto a una maggiore libertà di progettazione, la soluzione additiva ci ha permesso immediatamente di ridurre i tempi di realizzazione dei prototipi da diverse settimane a pochi giorni, comprimendo anche i costi complessivi grazie a un processo più semplificato ed economico”.
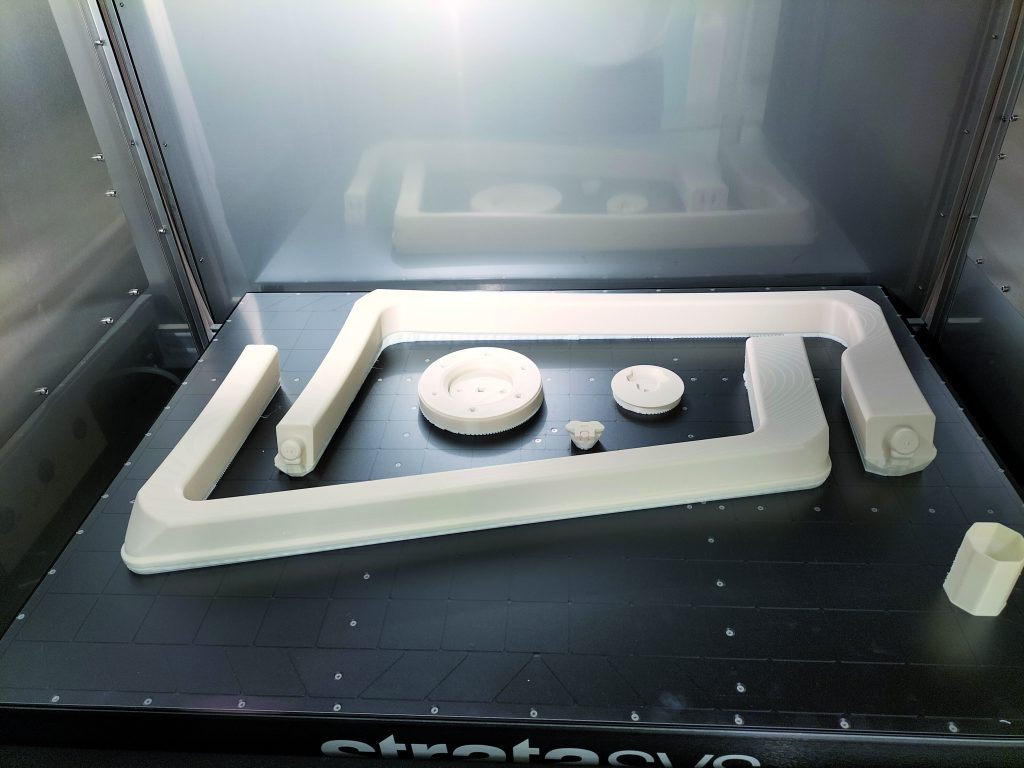
ragguardevole: 1000 x 610 x 610 mm.
Materiali resistenti
La resina fotopolimerica EPX 86FR è autoestinguente, rigida, dotata di resistenza meccanica e stabilità nel tempo; Carbon l’ha sviluppata per la realizzazione di parti finite, attrezzaggi e prototipi funzionali come cover, staffe e connettori per i settori auto e industriale tout court. Specializzata nella produzione di apparecchi per analisi di laboratorio, Astoria Pacific ha utilizzato il materiale per alloggiamenti di sistemi elettronici a regolazione fine per riscaldare, ad esempio, un bagno caldo o altro. “La difficoltà di approvvigionamento di PVC e lamiera metallica ci ha suggerito di sperimentare la piattaforma di Carbon con questo materiale ritardante di fiamma. Un cambiamento – spiega Whitney Menzel, Senior Engineer presso l’azienda – che ha ridotto i tempi di produzione da 18 a 2 settimane, compresso i costi, alleggerito i componenti, migliorato le prestazioni termiche e meccaniche”.
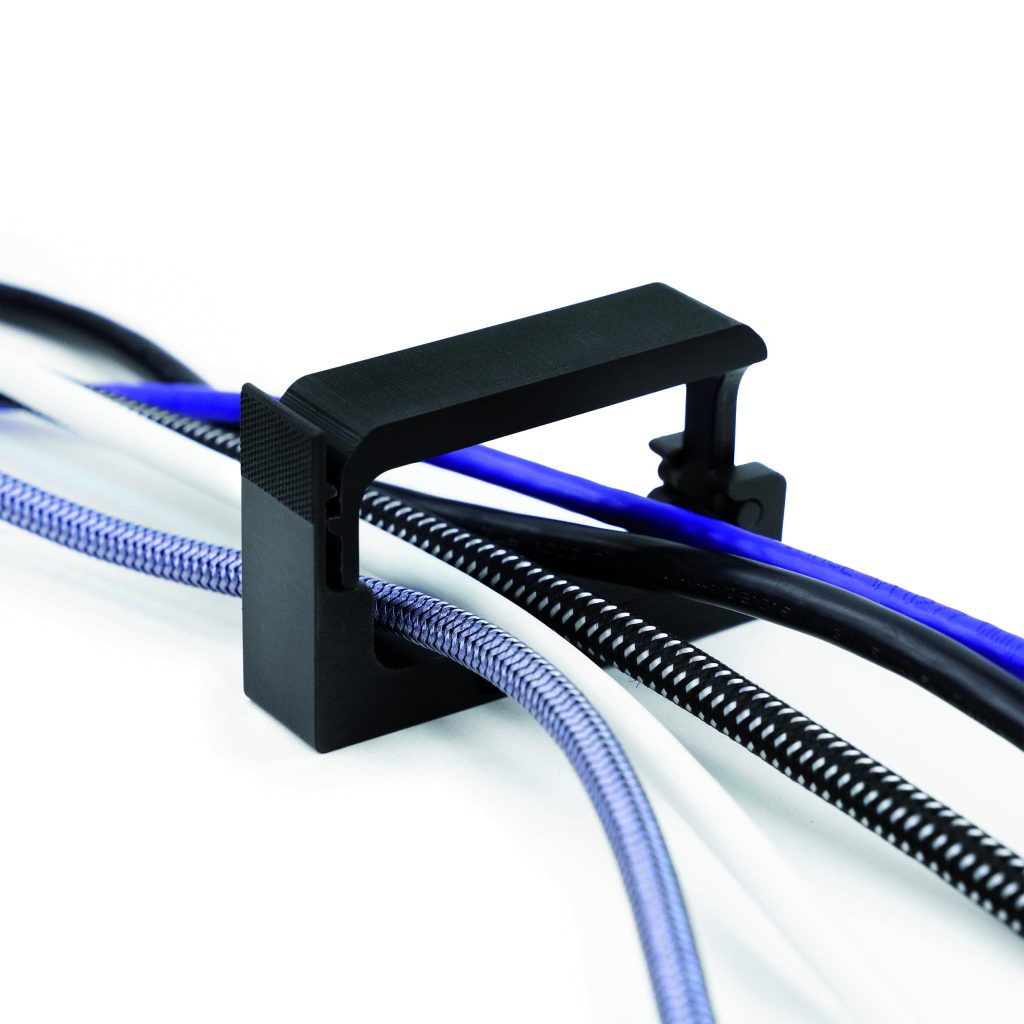
prototipi funzionali con prestazioni di sicurezza antifiamma in classe UL 94 V-0.
Un polietereterchetone rinforzato con fibre corte di ceramica che, più delle fibre di vetro o di carbonio, facilitano la stampa di geometrie complesse e spessori sottili, riducendo la rugosità e i difetti cristallografici: il filamento composito Helios PEEK 2005 di Roboze è studiato per garantire stabilità alle alte temperature e una buona finitura superficiale. Secondo l’azienda, riduce i tempi di post processing di oltre il 60% rispetto ad altri super polimeri e compositi; il rinforzo ceramico fornisce inoltre al composito prestazioni di isolamento termico anche a temperature superiori a 170°C e bassa conducibilità elettrica.
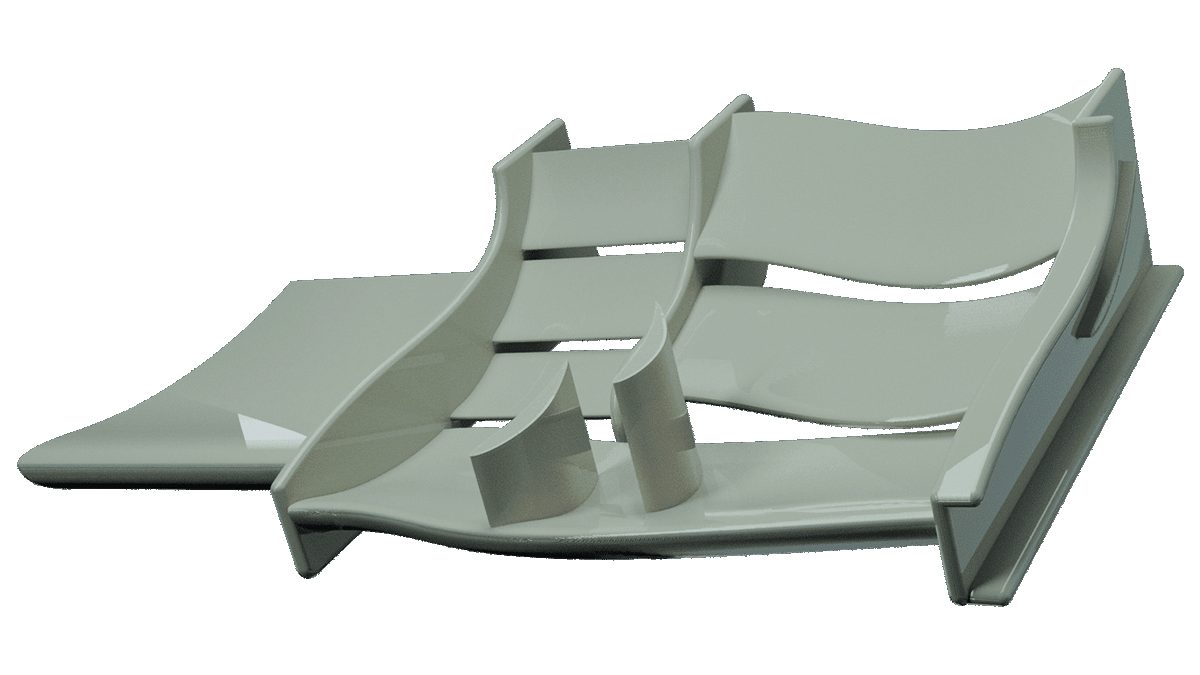
PEEK 2005 con rinforzo in fibre di ceramica: per componenti leggeri, robusti, isolanti.
Ultratenace, per impieghi industriali nella produzione di componenti funzionali con prestazioni elastiche, ridotto assorbimento di umidità, resistenza ad acidi, iglidur I10 di igus è un materiale per Sinterizzazione Laser Selettiva. È adatto per l’impiego in impianti e processi di galvanizzazione: i componenti stampati in 3D utilizzati nei processi di rivestimento per cataforesi devono resistere alle sostanze acide per ridurre al minimo il rischio di difetti e di possibili guasti. Il nuovo materiale è a norma FDA e conforme al Regolamento UE 10/2011, dunque idoneo al contatto con gli alimenti e indicato per applicazioni nell’industria alimentare e nel packaging. Igus fornisce la produzione on demand di parti stampate con tecnologia SLS in iglidur I10: i clienti devono solo inviare un file STEP con il modello 3D del componente desiderato e selezionare la quantità di parti e il materiale prescelto.
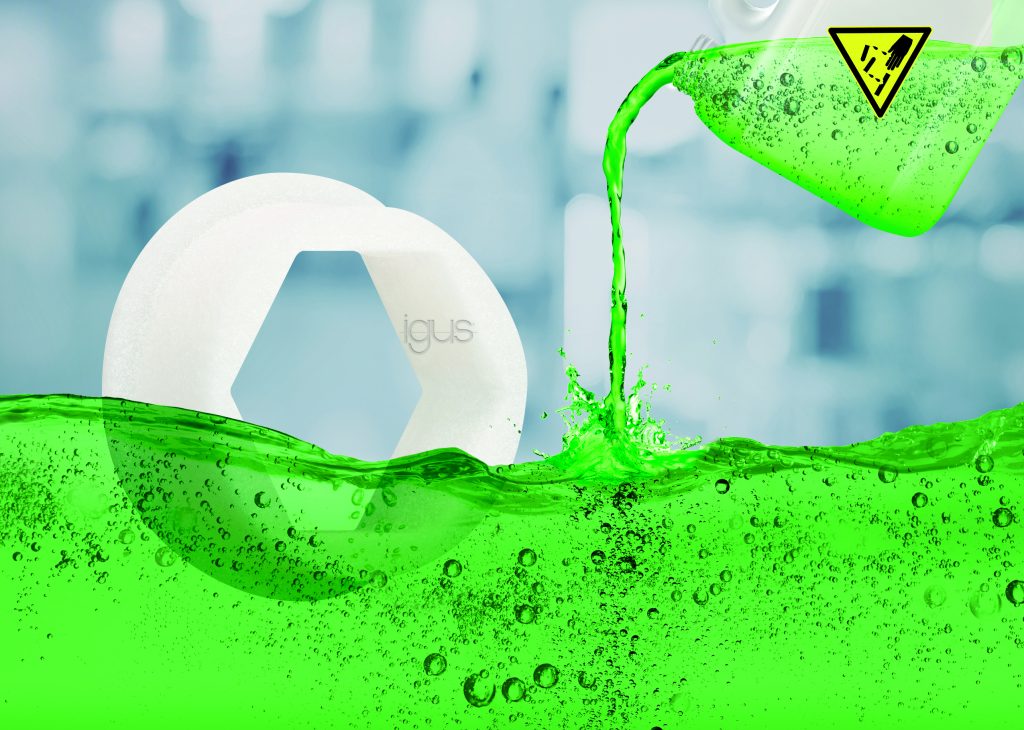
PEEK 2005 con rinforzo in fibre di ceramica: per componenti leggeri, robusti, isolanti.
A. F.
Nati dalla luce: DLP sempre più maturo
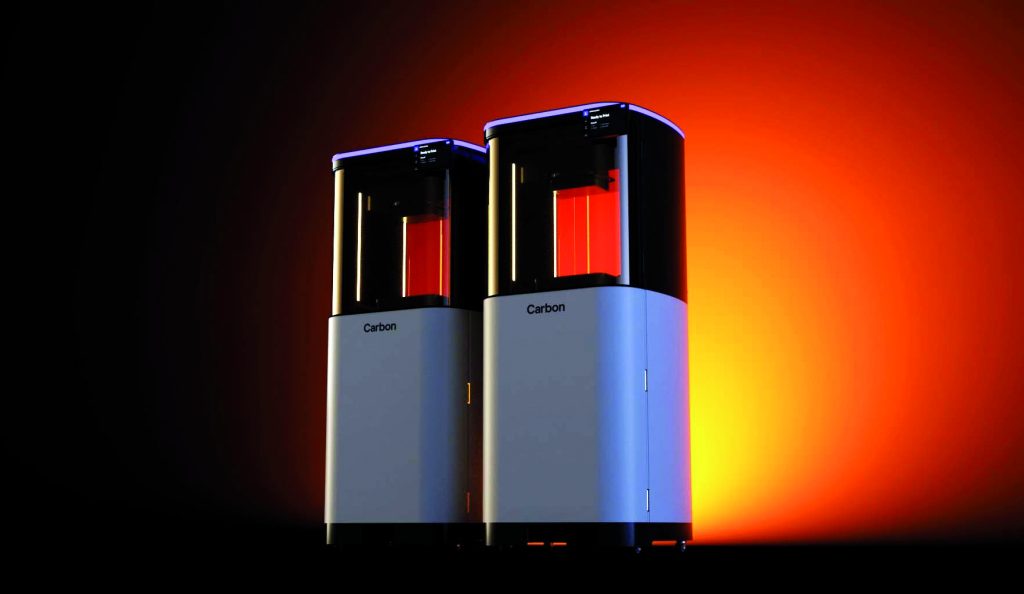
L’alta risoluzione di stampa e l’accurata finitura superficiale sono i punti di forza delle tecnologie di 3D printing SLA (stereolitografia) e DLP (Digital Light Processing). Ottimizzate nella velocità di stampa e nella disponibilità di resine di qualità industriale, le macchine di nuova generazione sono strumenti completi per prototipazione high-end in tutti i settori applicativi: dall’automotive ai beni di consumo, al dentale e al medicale. Due nuove stampanti con tecnologia DLP di Carbon, M3 e M3 Max, usano il software Design Engine per creare strutture lattice cruciali nell’ottimizzazione topologica delle parti. Una gestione a circuito chiuso dei carichi e della temperatura facilita l’utilizzo, migliora la ripetibilità dei pezzi stampati, permette di disporre di un’area di lavoro più ampia evitando surriscaldamenti e accelerando il processo. M3, disponibile dall’inizio di quest’anno, ha un volume di costruzione di 189 x 118 x 326 mm, ripetibilità di stampa con accuratezza fino a 37μm, finitura superficiale particolarmente uniforme e compatta. Nel modello M3 Max, atteso nel secondo semestre del 2022, la sorgente luminosa con risoluzione di 4K permette di ampliare il volume disponibile a 307 x 163 x 326 mm.