Come Kawasaki ha ottimizzato la produzione con le stampanti FDM.
Se i veicoli fuoristrada devono essere pronti a superare qualsiasi ostacolo, il percorso per il loro sviluppo non è da meno. Una grande varietà di sfide ingegneristiche richiede una flessibilità che spesso porta a una importante dipendenza dai fornitori di attrezzature e parti necessarie per la produzione.
Avvalendosi dei sistemi di Fused Deposition Modelling per grande formato di BigRep, distribuiti in Italia da MakeAdditive, Kawasaki è riuscita a rendere più efficiente e rapido lo sviluppo del nuovo prodotto.
AL RISPARMIO DI TEMPI E COSTI
Kawasaki ogni anno gestisce molti progetti per lo sviluppo di nuovi modelli e nelle fasi di prototipazione è importante riuscire a ridurre le tempistiche di realizzazione e i costi di attrezzaggio.
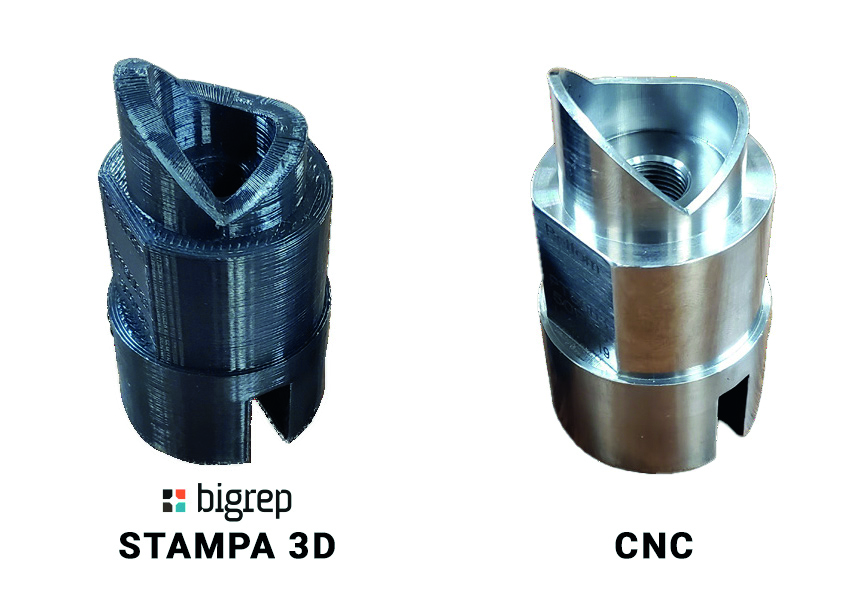
Un elemento fondamentale del prodotto è costituito dal telaio del veicolo che viene realizzato partendo da tubi grezzi lineari che vengono modellati attraverso un processo di piegatura a controllo numerico. Per riuscire ad ottenere le forme definite dall’ingegneria è indispensabile realizzare delle fixture particolari, delle dime per tenere in posizione e guidare i tubi durante la piegatura, che di norma sono prodotte da lavorazione meccanica e nel caso in questione approvvigionate in outsourcing.
Il processo in uso forniva certezza produttiva ma tempi e costi non più competitivi con le moderne esigenze di sviluppo. Kawasaki ha quindi coinvolto BigRep richiedendo supporto per velocizzare il processo di prototipazione.
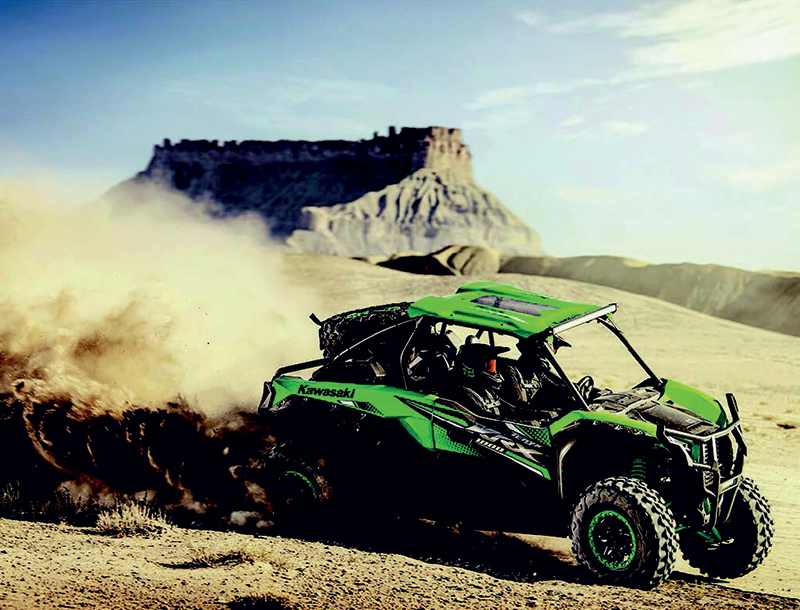
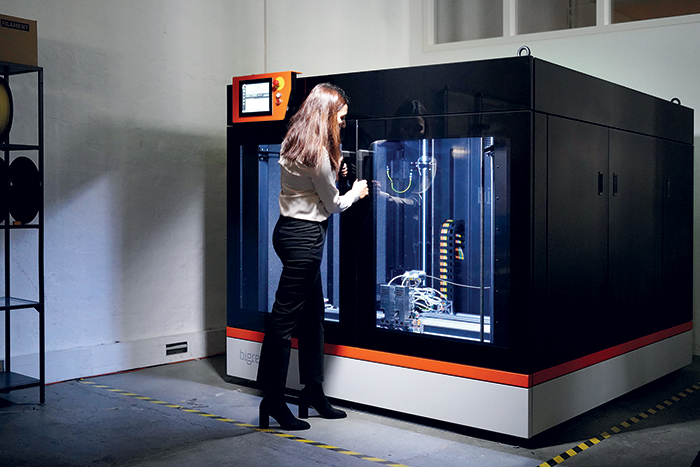
UN PARTNER RISOLUTIVO
Analizzando le pinze piegatrici in uso è stata effettuata una verifica nella gamma di materiali disponibili e si è visto che questi particolari potevano essere prodotti utilizzando l’HITEMP-CF, un tecnopolimero con una piccola carica di carbonio dalle buone caratteristiche meccaniche.
L’ulteriore elemento per velocizzare il processo è stato costituito dall’adozione di una stampante industriale, la BigRep PRO, direttamente in linea di prototipazione. Grazie all’adozione del nuovo processo e dei nuovi materiali è oggi possibile per Kawasaki seguire le richieste di modifica progettuali in tempi rapidi, realizzando al contempo un significativo risparmio economico, passando in media dai 500 ai 17 euro per ogni dima e una riduzione di tempo da due settimane a un giorno.
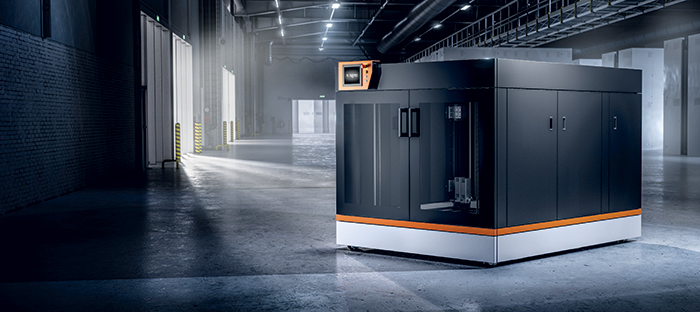
https://www.linkedin.com/company/makeadditive/
Per approfondire:
Giovedi 23 nov 11:00 -12:00
WEBINAR: Massimizza l’efficienza produttiva con BigRep
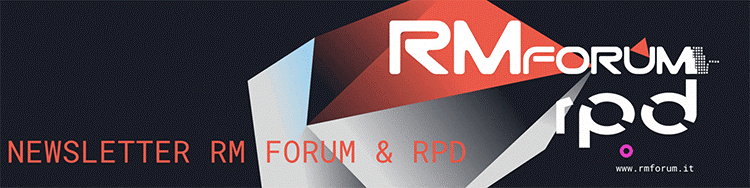
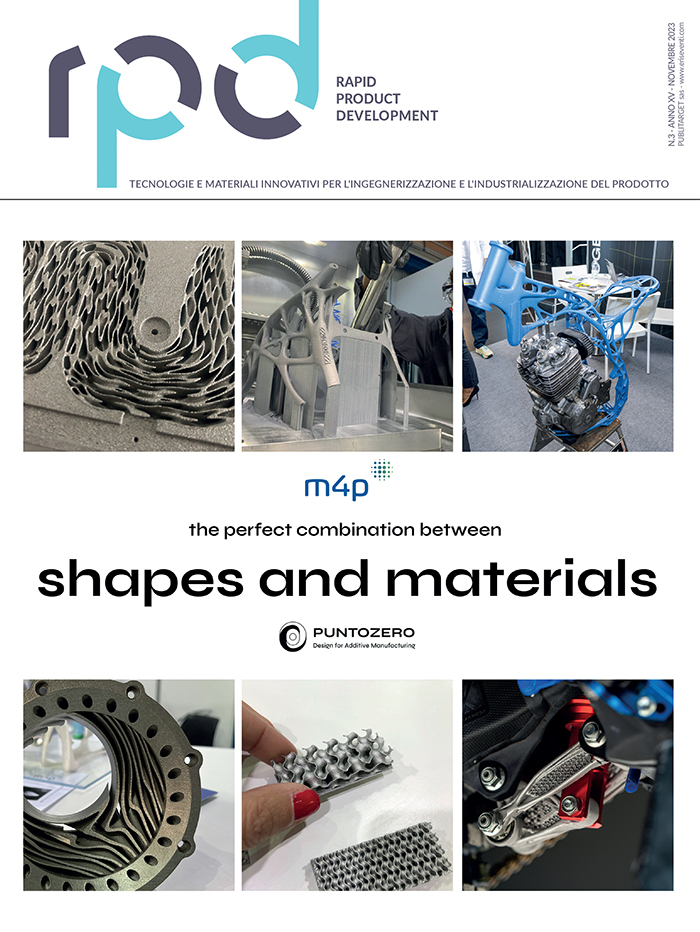
LEGGI L’ULTIMO NUMERO DI NOVEMBRE DI RPD
https://www.sfogliami.it/fl/283822/txmm9c77h538nykryzgp14683esfe1